Asphalt plants are key in making materials for roads and upkeep. This guide covers all you need to know about how they work and the equipment used. It’s vital for contractors, engineers, and policymakers to understand this well.
This guide focuses on the role of aggregates, asphalt binder, and fillers in making quality asphalt. The U.S. is the biggest asphalt producer, followed by China. It also offers tips on keeping production efficient and following environmental rules.
Explore additional insights as we look at different asphalt plant types. We’ll also dive into the asphalt production process.
Table of Contents
Introduction to Asphalt Plants
Asphalt plants are key in the construction and infrastructure world. They mix asphalt, which is vital for roads. This process is essential for building and fixing roads.
The making of asphalt starts with raw materials like aggregates and bitumen. These must be mixed just right to meet quality standards.
Knowing how asphalt plants work helps with planning projects. The market for these plants is growing fast. In 2020, it was worth $6.77 billion and is expected to reach $7.41 billion by 2027.
East Asia is leading the market, with 30% of sales. North America and Europe are also growing quickly.
Asphalt plants vary in size, from CFB80 to CFB400, and JNW180 to JNW340. They use different mixers for different types of asphalt. This meets various construction needs.
These plants make different kinds of asphalt. There’s hot mix for durability, warm mix for saving energy, and cold mix for cheap repairs. Mobile plants, like the ALmix Travel Pack series, are great for moving and setting up fast.
Asphalt plants are vital for road construction. They ensure projects are done well and last long.
Importance of Asphalt in Road Construction
Asphalt is key in road building, making roads strong and efficient. Over 94% of paved roads in the U.S. use asphalt. This shows its wide use and success as a paving material.
This material is flexible, handling heavy loads and weather changes well. It’s also waterproof, preventing water from pooling on roads. This helps roads last longer with the right care, thanks to strong bonding from bitumen production.
Asphalt also has environmental benefits. Almost 100 million tons of recycled asphalt are used in new roads each year. Recycling asphalt and using old tires in paving mixtures saves resources and reduces waste.
Warm Mix Asphalt (WMA) production has grown a lot, up by 67% from 2010 to 2011. This eco-friendly option cuts down on emissions and makes paving easier, extending the paving season.
Asphalt is not just practical but also vital for road projects. It’s affordable, easy to install, and can be recycled. This makes asphalt a top choice for building lasting infrastructure that meets today’s needs.
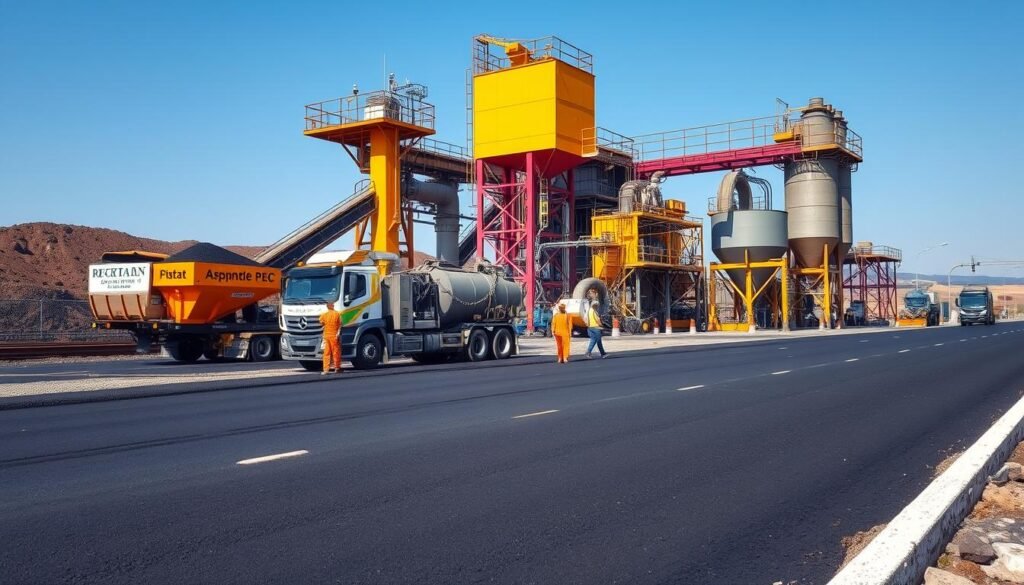
Types of Asphalt Plants
Asphalt plants are key in making asphalt for roads. You can pick from batch, drum, or counterflow plants based on project size and output needs.
Batch Asphalt Plants
Batch plants are great for smaller projects. They make asphalt in batches. The process includes feeding aggregates, drying, screening, mixing, and storing.
These plants can handle different mix designs. This makes them flexible for various asphalt needs. The LB Series Asphalt Batch Mix Plant is a top choice, with capacities from 60 t/h to 400 t/h.
Drum Asphalt Plants
Drum plants are good for big projects. They mix and dry asphalt continuously. This makes them fast and efficient.
They mix aggregates with bitumen in the drying drum. This makes asphalt production smooth and quick.
Counterflow Asphalt Plants
Counterflow plants are a step up from drum plants. They mix aggregates and hot gases in opposite directions. This makes better asphalt and saves energy.
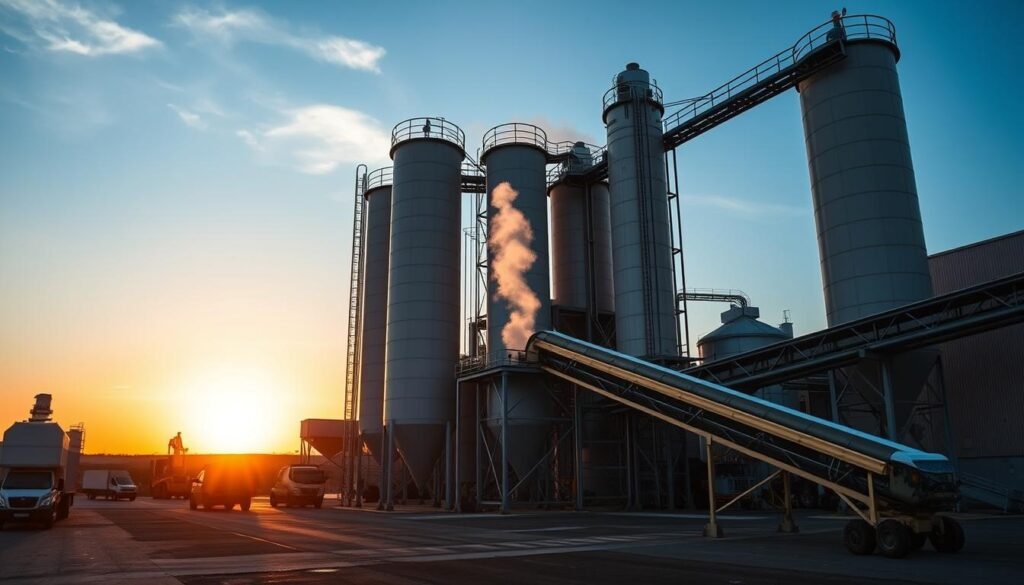
Asphalt Plant Type | Production Method | Capacity Range (t/h) | Best Suited For |
---|---|---|---|
Batch Asphalt Plant | Discrete batches | 60 – 400 | Small to medium projects |
Drum Asphalt Plant | Continuous | 20 – 100 | Large projects |
Counterflow Asphalt Plant | Continuous | 60 – 160 | High-quality asphalt needs |
Choosing the right asphalt plant depends on project needs, output, and budget. Knowing the benefits of each type helps make a smart choice for efficient asphalt production.
Understanding Asphalt Production Processes
The asphalt production processes are key to making top-notch paving materials. In the United States, about 18 billion tonnes of asphalt are used yearly. Around 94% of roads have asphalt surfaces.
This process starts with aggregate processing. It involves getting and preparing the raw materials for asphalt mixtures. Asphalt mix usually has 5% asphalt cement and 95% aggregate.

First, the aggregates go through different stages to get the right size and consistency. Then, they are dried and heated to remove moisture. This makes them stick well when mixed with bitumen.
Bitumen production is vital for asphalt’s performance. It’s kept at 155-160°C in heated tanks. After that, the components are mixed to create hot mix asphalt (HMA) or cold mix asphalt (CMA).
Hot mix asphalt is made at 200 to 350 degrees Fahrenheit. Cold mix asphalt, with lower costs and less heating, uses a special oil blend to keep water out for repairs.
When you look at asphalt production, think about its impact on the environment. The asphalt industry recycles old pavement, with at least 90 million tons reused each year. This helps the environment.
Companies like Wolf Paving recycle 100% of their removed asphalt. This shows their dedication to reducing waste and improving resource use.
The asphalt production processes are complex. They involve careful material handling, precise temperature control, and a focus on sustainability. Knowing these steps shows how important each phase is in making quality asphalt for our roads.
Aggregate Handling and Storage
Effective aggregate handling and storage are key in asphalt production. Using the right storage systems and handling methods ensures the quality of materials. This affects the final asphalt product’s performance. This section covers important aspects of aggregate storage systems and handling processes.
Aggregate Storage Systems
Many aggregate storage systems help keep materials quality high. Some common ones are:
- Cold feed bins: Great for storing different aggregate sizes separately.
- Silos: Keep aggregates safe from moisture and contaminants.
- Fabric structures: Offer good ventilation and can be up to 300’ wide, providing plenty of space for storage.
Using climate-regulating fabric covers is beneficial. They protect aggregates from rain and snow. This helps keep them in good condition, reducing the need for extra asphalt processing.
Aggregate Handling and Conveying
Efficient aggregate handling uses various techniques for transporting materials. Key methods include:
- Conveyor belts: Move aggregates smoothly and continuously.
- Feeders: Provide a steady supply to production lines.
- Elevators: Help move aggregates vertically between storage levels.
Effective stockpile management is vital. This includes using proper construction techniques, like sloping surfaces 2% to 4% to prevent moisture buildup. Regular monitoring of moisture content by suppliers and operators helps maintain quality and efficiency.
Aggregate Handling Method | Benefits | Challenges |
---|---|---|
Conveyor Belts | Smooth transport and reduced labor costs | Regular maintenance needed to prevent breakdowns |
Feeders | Consistent material flow ensures accurate batching | Can be subject to blockages or wear over time |
Elevators | Efficient vertical movement of heavy materials | Requires careful installation and maintenance |
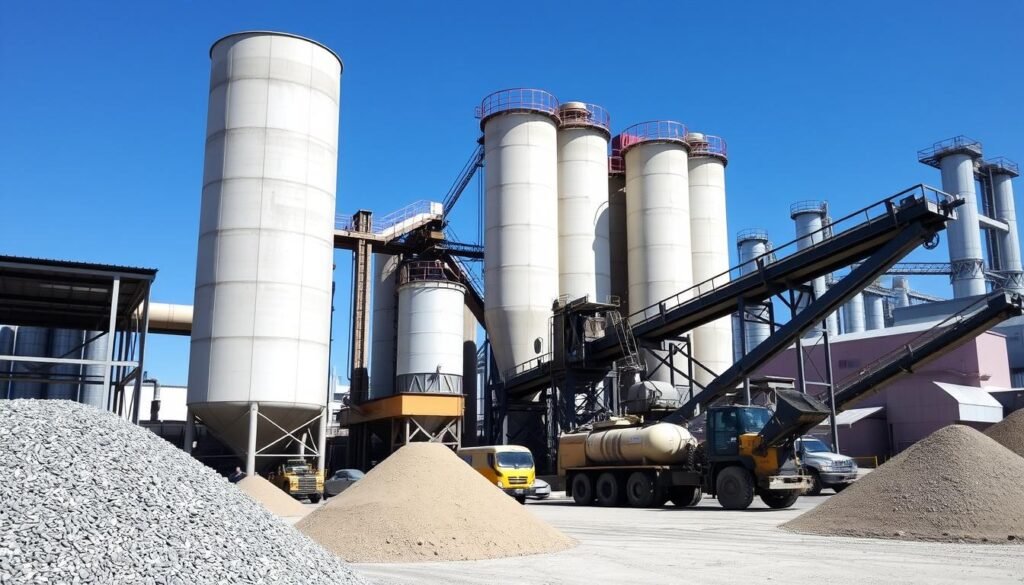
Drying and Heating of Aggregates
Drying aggregates is key for making good asphalt. Too much moisture can make the asphalt weak. This weakens the road. We’ll look at why removing moisture is important and the different dryers used.
Purpose of Drying Aggregates
Drying aggregates is very important. It makes the asphalt stronger by removing moisture. Even a small amount of moisture can affect how well the asphalt is made.
By drying the aggregates well, you get better asphalt. This makes the roads last longer and work better.
Types of Aggregate Dryers
There are many types of dryers for aggregates. Knowing about them helps you choose the best one for your needs. The main types are:
- Parallel-Flow Drum Dryers: These dryers move aggregates and exhaust gases in the same direction. This helps heat transfer well. The cold-feed bins help mix the materials right.
- Counter-Flow Drum Dryers: In these dryers, exhaust gases move against the aggregates. This keeps the heat in better and removes moisture well.
- Batch Aggregate Dryers: These are used in batch plants. They dry small amounts of aggregates for each mix cycle.
There are three main things that affect drying aggregates well. These are how much heat the aggregates take, the temperature difference, and how long they are exposed. Other things like moisture, flame position, and aggregate size also play a part.
Improving these factors can make drying aggregates more efficient. Longer drying times help remove more moisture. This means the asphalt can be made at higher temperatures, which is good for making asphalt.
Knowing about these factors and types of dryers can make your asphalt plant better. This leads to better asphalt. For more on managing aggregates, check out this for tips on growing and handling materials well.
Type of Dryer | Efficiency | Heat Transfer Direction |
---|---|---|
Parallel-Flow Drum Dryer | Moderate | Same Direction |
Counter-Flow Drum Dryer | High | Opposite Direction |
Batch Aggregate Dryer | Variable | N/A |
Mixing Processes in Asphalt Plants
Asphalt plants use two main mixing methods: batch mixing and continuous mixing. Knowing these processes is key to making high-quality asphalt. Batch mixing, or tower asphalt plants, mixes materials in batches. This method ensures precise control and quality in the hot mix asphalt.
Continuous mixing plants, on the other hand, are great for making lots of asphalt quickly. They dry and mix aggregates at the same time, making the process faster. These plants are good for big projects because they keep producing at a steady rate. Even though batch mixing might make better asphalt, continuous mixing plants can make more of it.
Both types of plants have important parts that help with mixing. Batch plants have bins for cold aggregates, drying drums, and a mixing unit. Continuous plants have a slinger conveyor belt and a drying/mixing drum. These parts are vital for making efficient and quality asphalt.
Getting the right amounts of aggregates, bitumen, and filler is very important in asphalt mixing. Accurate measurements mean consistent mixtures that meet high standards. Also, using reclaimed asphalt pavement (RAP) makes production more sustainable. For more on asphalt production, check out this resource.
Mixing Process | Batch Mixing | Continuous Mixing |
---|---|---|
Production Type | Batch Size (4-8 tons) | Continuous Process |
Quality | Higher Quality Hot Mix Asphalt | Efficient Production Rates |
Components | Cold Aggregate Feeder, Drying Drum, Mixing Unit | Cold Aggregate Feeder, Slinger Conveyor, Mixing Drum |
Production Capacity | 60-260 tph | Higher Capacity |
Storage and Transport of Asphalt Mixture
Keeping asphalt mixtures in top shape is key for good pavement. After making it, keeping it warm and soft is very important. Heated silos help a lot with asphalt mixture storage, keeping it ready for transport. Knowing how to do this right is very important for a project’s success.
Finished Asphalt Mix Storage
After making asphalt, it needs to be stored well to stay good. Heated silos are used, each for different mixes. For example:
Type of Mixture | Maximum Storage Time |
---|---|
Superpave | 18 hours |
Stone Matrix Asphalt | 3 hours |
Open-Graded | 2 hours |
Managing asphalt mixture storage carefully stops it from getting worse. This makes sure it’s ready for use when it gets to the job site. Following these storage times keeps the material in top shape and improves its performance.
Transporting Asphalt to Job Sites
Then, asphalt is moved to where it needs to be. Getting it there fast and well is very important. When you transport asphalt, you need the right haul vehicles to keep it warm.
Working well between storage and job sites is key for quick delivery. Moving asphalt right means haul vehicles must keep it warm all the way. This keeps the quality high.
For more tips on asphalt storage and handling, check out this detailed overview.
Innovations in Asphalt Plant Technology
The asphalt industry is seeing big changes to make it more efficient and green. New technologies are being used to recycle materials and cut down on harmful emissions. This shift is driven by the need for eco-friendly practices.
Recycling and Sustainability
Now, asphalt plants can use up to 100% recycled asphalt in their work. This not only cuts down on the need for new materials but also reduces waste. The use of porous asphalt is also growing, with 56% of new products being this type.
Companies like Ammann and Marini are leading the way. They make machines that can handle recycled asphalt efficiently. For example, Ammann’s RSS 120-M can make 120 tonnes of recycled asphalt per hour.
Emission Control Systems
Modern plants are also focusing on reducing harmful emissions. Baghouse filters are key in cutting down dust and harmful gases. These systems work well, keeping production efficient while meeting air quality standards.
Other innovations, like warm mix asphalt, help lower energy use and emissions. Companies like Astec are working on making plants more automated. This not only saves on labor costs but also improves safety.
Innovation | Description | Benefits |
---|---|---|
100% RAP usage | Incorporating recycled asphalt in new mixtures | Reduces waste and reliance on virgin materials |
Baghouse filters | Dust and VOC emission control | Improves air quality without hindering operations |
Warm mix asphalt | Lower production temperatures | Decreases energy use and greenhouse gas emissions |
Automation | Automated systems for plant management | Enhances efficiency and safety |
Maintaining Asphalt Production Efficiency
Keeping asphalt plants running efficiently is key in today’s market. Regular asphalt plant maintenance boosts efficiency and meets customer quality needs.
Keeping the plant site clean is essential. It improves efficiency and reduces safety risks. Clean equipment lasts longer and is easier to maintain.
Setting aside maintenance days helps avoid interruptions. It also extends the plant’s life. Proper storage and moisture control of aggregates ensure quality hot mix asphalt and lower fuel use.
Regular inspections and timely part replacements keep the plant running well. Insulation reduces heat loss and energy use. Tuning and maintaining burners for fuel efficiency is also important.
Using high-quality, clean fuel improves burner performance and cuts emissions. Regular checks on electronic parts prevent downtime and extend the plant’s life.
Accurate weighing through scale calibration is key for reliable asphalt mixes. A good training and safety plan boosts efficiency and safety.
Regular audits help find ways to improve efficiency. Happy employees lead to better productivity. Choosing and rewarding the right workers is important.
Investing in technology and sustainability is part of a long-term strategy. AIMIX asphalt plants support high production volumes. They offer both stationary and mobile plants for flexibility.
AIMIX plants use energy-efficient technologies to cut costs and maintain consistency. Their support services ensure plants run smoothly, highlighting the need for regular maintenance.
This focus on quality helps plants meet strict standards. As costs rise, managing efficiency is critical for survival. By following these steps, plants can boost productivity and meet industry and environmental goals.
For more on improving asphalt plant efficiency, visit this link.
Conclusion
Asphalt plants play a key role in road construction. They use modern tech, like AIMIX asphalt plants, for efficient and green operations. These plants have automated systems for precise mixing and temperature checks. This ensures top-notch asphalt for all kinds of paving needs.
Quality control is a big deal in asphalt production. AIMIX’s recycling systems help use old asphalt again. This makes roads last longer and is better for the planet. It’s a win-win for everyone.
Knowing about these technologies is important for the asphalt industry. Choosing AIMIX asphalt plants boosts efficiency and quality. It also shows you care about the environment in every project.